Design and Analysis Solutions & Services for Automobile Segment
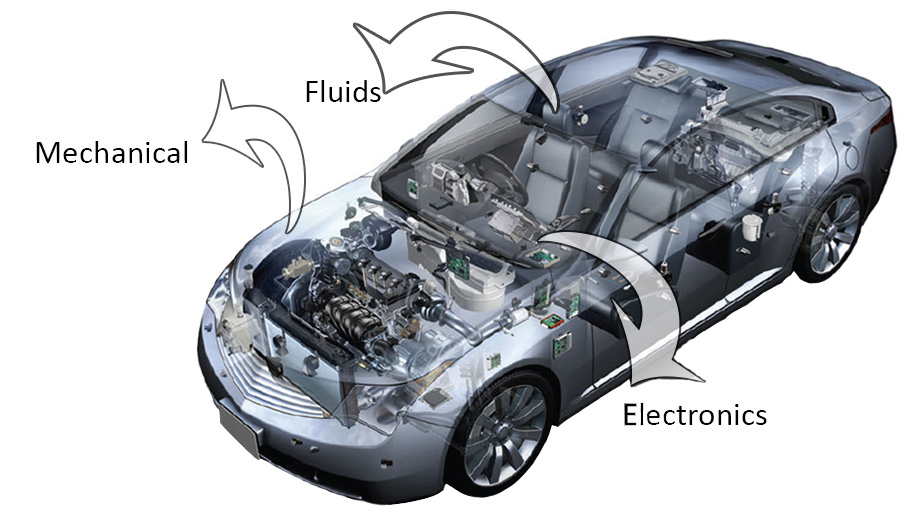
- STRENGTH ANALYSIS
- VIBRATION
- THERMAL ANALYSIS
- DURABILITY
- RIGID BODY DYNAMICS
- HYDRODYNAMICS
- COMPOSITES
- IMPACT
- OPTIMIZATION
- HPC FOR FEA
- TOPOLOGY OPTIMIZATION
- ADDITIVE MANUFACTURING
- CAVITATION
- FLUID–STRUCTURE INTERACTION
- HIGH RHEOLOGY MATERIAL
- HPC - FLUIDS
- MULTIPHASE FLOWS
- REACTING FLOWS AND COMBUSTION
- SHAPE OPTIMIZATION
- SIMULATING AIRCRAFT ICING
- SINGLE PHASE, NON REACTING FLOWS
- THERMAL MANAGEMENT
- TURBOMACHINERY
- TURBULENCE MODELING
- ANTENNAS
- ELECTRIC MOTORS
- ELECTRONICS COOLING
- LOW-FREQUENCY ELECTROMAGNETICS
- POWER ELECTRONICS
- POWER INTEGRITY
- RF AND MICROWAVE
- SIGNAL INTEGRITY
India was the fourth largest car manufacturer in the world in 2017. Indian auto manufacturers produced a record 29.1 milion motor vehicles in 2017-18 (Apr-Mar). With such a growing market Entuple is all set to provide its expertise in the Automotive segment.
Entuple can provide its design and analysis capability on Ansys for automotive mechanical components, antennas, electronics, aerodynamics & also provide its valuable expertise on multi-physics problems.
STEERING YOUR BUSINESS TOWARD SUCCESS
In a range of applications, ANSYS helps automotive companies speed ahead of competitors with rapid product and process design.
Being first to market is synonymous with success. Automotive companies that lead in anticipating and meeting market needs will emerge as winners, while others struggle to catch up. But you cannot afford to sacrifice product confidence for speed. In an industry characterized by well-known product recalls, your engineering team must combine speed with a strong commitment to deliver on your product promise.
Whether your organization is in an emerging or a mature market, an OEM or a supplier, ANSYS software provides the proven capabilities to help meet the challenges at hand. Our tools have already supported the rapid launch of countless innovative automotive products and processes.
ANSYS: Kick-Starting Innovation in Diverse Applications
Consumer, regulatory and market pressures exist in diverse segments ranging from passenger cars to Formula 1® race cars, construction vehicles, commercial trucks, tractors, motorcycles and locomotives.
Auto developers use ANSYS solutions to develop engines that burn fuels more efficiently, rely on alternative energy sources or incorporate next-generation emissions control devices. By delivering multiphysics capabilities in a single platform, we make it easier for your engineering team to examine the complex issues surrounding engine performance and outputs.
Our tools have been central in advancing industry “lightweighting” initiatives that focus on the use of novel composite materials to optimize a variety of components and reduce overall fuel consumption.
Innovators apply ANSYS to highly specialized problems such as brake squeal in passenger cars and noise, vibration and harshness. By illuminating the causal factors behind complex physical phenomena, our solutions help engineering teams increase product reliability and minimize costly manufacturer recalls. Whatever the pressing competitive issue - from body to transmission to interior - ANSYS delivers broad simulation capabilities and deep automotive expertise to help your business emerge as the next industry success story.
Bühler Motor used ANSYS tools to develop mechatronic DC drives and gear motors, systematically analyzing and optimizing different components to reach the highest possible optimization level while also meeting safety standards.
“The ease of using ANSYS simulation tools has helped to transform our organization from a test-centric culture to an analysis-centric culture”
“When you design innovation, you can’t design in just one area — you have to couple everything at the early stage of the project. And we found that ANSYS enables us to do that.”
General Motors, ANSYS and the University of South Carolina are working together to develop CAE design tools that accurately represent multiphysics phenomena across a wide range of scales for cells and packs, funded by an award from the U.S. Department of Energy’s National Renewable Energy Laboratory. The project will contribute to making HEV/EV batteries more affordable, better performing and longer lasting.
ANSYS: ADDRESSING CHALLENGES FROM BUMPER TO BUMPER
From aerodynamics and thermal management to engine design, durability and NVH, our products and application knowledge can help you understand product performance long before a prototype is ever built.
We have worked aggressively to assemble our technology suite so that you can address the wide range of complexities and transform your organization into an innovator. Our CFD products include advanced turbulence models to help optimize aerodynamic performance of vehicles. Our structural solutions incorporate nonlinear, fatigue and rigid-body dynamics tools to support development of composites and other new materials. You can tightly couple a number of products to assess traditional engine technologies as well as fuel cells, hybrid–electric engines and other emerging technologies.
Passenger cars are on the verge of becoming more electric than mechanical in nature. We have the clear leadership in electromagnetics simulation to support revolutionary developments — as well as the multiphysics capabilities to optimize component interaction with other systems.
Automotive engineers consider complex real-world physics interactions and make valueadded design trade-offs. Every day, and in every automotive segment, they use industry-leading multiphysics tools from ANSYS to position their companies for innovation leadership.
The Engine NVH Analysis Section at Ford Motor Company used ANSYS software to conduct design-of-experiments studies, gaining insight into modal and vibrational response, radiated noise, and crank/block dynamic interactions.
Almost half the value of next-generation automobiles will come from onboard electronics and electromechanical components. These devices must survive in harsh operating conditions, such as significant swings in humidity levels. Product developers can apply our tools to incorporate effects such as Joule heating phenomena in package or board substrates.
The automotive global supply chain is crowded with OEMs and multi-tier suppliers. ANSYS provides tools to address their varied design issues — and to manage the huge amount of data that simulation generates. The result: fewer surprises when components and systems are assembled into a finished vehicle.
THE FUEL-EFFICIENT GEEC
The Galway energy-efficient car (better known as the Geec) is a battery-powered electric eco-car designed and built by engineering students from National University of Ireland Galway to complete in the Shell Eco-marathon Europe. The event’s goal is not speed (although cars must travel an average of 25 km/hour) but completing an 18 km urban street circuit using the least amount of fuel or energy. Simulation with ANSYS helps NUI Galway achieve efficiency gains with simulation in two major areas: aerodynamics and structural weight. The team used ANSYS computational fluid dynamics to minimize aerodynamic drag, which accounts for about one-third of all energy consumption in a highly optimized car. Students investigated many design concepts, with the objective to make manufacturing easier and improve aerodynamic performance.
Simulation results delivered drag forces as well as visualizations to provide insight into sources of drag and guide geometric design changes. The group simulated successive iterations of the chosen concept to approach a high-performance surface shape. Because constructing physical models for testing is cost-prohibitive, simulation was the only way to converge on an optimal shape. The Geec is wider across its front wheels than most vehicles participating in the competition, but analysis (supported by simulation) showed that improved cornering at speed outweighed the aerodynamic disadvantage. Using ANSYS CFD, the team greatly improved the aerodynamics of the 2016 Geec. The 2015 car had exposed wheels and a simple body with a flat floor. The new car’s wheels are fully enclosed with the body elevated above the ground. The concept is based on an airfoil, but the detailed shape is a product of simulation. Weight is a major factor in tire and bearing rolling resistance, which accounts for almost two-thirds of energy consumption.
The team used ANSYS Mechanical to support the design of various components – for example, to determine how much material could safely be removed from a large sprocket. But the team’s biggest change in lightweighting is reserved for the future: The 2017 or 2018 car will have a monocoque design. The 2016 car incorporated a nonstructural carbon-epoxy body over an aluminum alloy frame. Team members working on the future carbon-fiber monocoque design use ANSYS Composite PrepPost (ACP) to create a realistic layup and employ ANSYS Mechanical to apply loading conditions that replicate those during qualification and under driving conditions. Students determine where additional material might be needed and where wall thickness can be minimized to save weight. The ANSYS Workbench interface makes it quick and easy to strengthen the monocoque in particular areas, and then determine if those changes provide overall improvement in structural integrity. The process will enable NUI Galway to reduce the car’s weight by about 10 kg to 15kg as it attempts to match weight with the best cars in the competition.